Il costo “vero” del prodotto 2022
Il presente articolo ha lo scopo di riproporre un precedente articolo di questo sito, denominato “il costo vero del prodotto” rivisitato e corretto in ottica presente, con i nuovi fattori destabilizzanti che stanno influenzando i costi della maggior parte dei prodotti realizzati dalle aziende italiane.
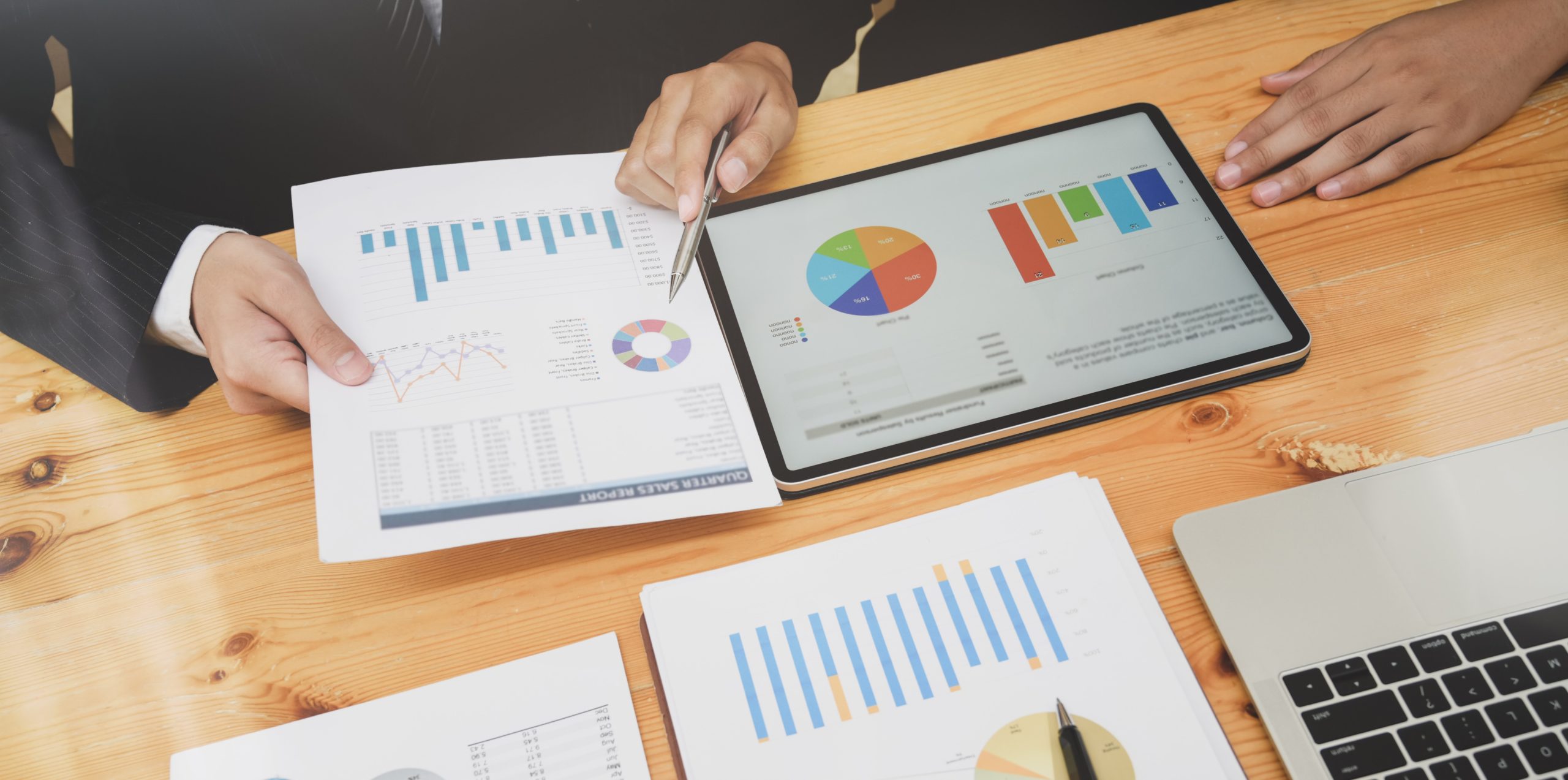
Mi riferisco in particolare all’aumento dei prezzi della materia prima ed all’aumento dei costi dell’energia, già rilevati nel post-pandemia (o meglio post “prima ondata”), che ora – a causa della guerra in Ucraina – assumono valori non solo molto più elevati rispetto al passato, ma presentano anche una notevole variabilità nel breve periodo.
In questi tempi di crisi internazionale e di ripresa (almeno in alcuni settori) è molto importante riuscire a valutare nel modo corretto il costo reale del prodotto, soprattutto per la piccola e media impresa (PMI). Ciò serve ad una serie di scopi che possono essere riepilogati nei seguenti:
- Stabilire un giusto prezzo da proporre nell’offerta al cliente;
- Valutare la remuneratività di una determinata commessa;
- Fornire alla contabilità analitica uno degli elementi fondamentali per il controllo di gestione.
Oggi a tali obiettivi se ne aggiunge un quarto, ovvero essere in grado di riformulare rapidamente il costo (ed il prezzo) del prodotto a fronte della variabilità di alcuni fattori che contribuiscono ad esso (nella fattispecie costi della materia prima e dell’energia), al fine di essere reattivi nel rispondere a qualunque cambiamento al contesto di riferimento.
Se esaminiamo il caso della determinazione del costo del prodotto in un’industria manifatturiera, in particolare in un’azienda meccanica che realizza prodotti meccanici finiti, possiamo identificare una serie di problematiche connesse al costo del prodotto ed anche alcuni errori che vengono sistematicamente commessi da piccole (e talvolta anche medie) imprese del settore meccanico.
Innanzitutto, identifichiamo le componenti che determinano il costo del prodotto. Per semplicità consideriamo un prodotto/componente con distinta base mono-livello, ovvero non costituito da componenti che debbano essere realizzati o acquistati individualmente e poi assemblati fra loro per formare l’assieme. Tale semplificazione – a parte il fatto che non ci costringe a considerare una distinta base a più livelli del nostro prodotto – non comporta alcuna differenza nell’analisi dei concetti fondamentali su cui si basa il costo del singolo componente, infatti, nel caso di prodotto costituito da più componenti, sarà sufficiente sommare i costi dei singoli componenti per determinare il costo dell’assieme realizzato assemblando tutti i componenti di cui è composto.
La teoria della determinazione del costo del prodotto ha individuato due tecniche di aggregazione dei costi ben distinte: il criterio del costo pieno (full costing) ed il criterio del costo variabile (direct costing). Nessuno dei due è valido in assoluto, entrambi hanno pregi e difetti. Soprattutto, le informazioni offerte dai due metodi sono molto differenti.
L’approccio più corretto nel calcolare i costi è quello di utilizzare il full costing o il direct costing in funzione della decisione da prendere. Il che è quello che viene generalmente fatto, magari senza rendersene conto, da coloro che non posseggono un sistema formalizzato di Contabilità Analitica.
Il full costing fornisce un’immagine immediata del costo totale dell’oggetto analizzato (nel nostro caso il prodotto). Questa metodologia è ampiamente accettata: ai costi diretti dell’oggetto (materie prime, manodopera, consumi diretti) si somma una quota “convenzionalmente congrua” dei costi indiretti (ammortamenti, costi commerciali, costi distributivi, spese generali) in modo tale da configurare un costo totale.
Il direct costing, d’altro lato, è una metodologia di calcolo più moderna, nei sistemi di Contabilità Analitica, che consiste nel considerare i costi fissi non come costi da imputare al singolo prodotto, ma piuttosto come costi di periodo che devono essere necessariamente coperti per raggiungere un pareggio economico. Al prodotto vengono imputati solamente quei costi che gli sono oggettivamente riferibili, cioè i costi variabili.
Accanto a queste due tecniche tradizionali si è aggiunta la metodologia dell’ABC Costing (Activity Based Costing), basata sull’assorbimento di risorse (e di costi) da parte di attività che poi permettono di realizzare il prodotto.
Se un piccolo imprenditore avesse voglia di leggersi uno dei tanti testi teorici sulla contabilità analitica e sul controllo di gestione al fine di determinare il costo del prodotto si troverebbe disorientato dagli esempi proposti nella letteratura che prendono in esame la produzione di pochi prodotti con volumi ben determinati. La realtà della piccola impresa del nostro esempio è ben diversa: il costo presunto del prodotto deve essere determinato in fase di formulazione del preventivo, quando i volumi di produzione non sono ancora ben noti ed i tempi di realizzazione del particolare possono solo essere stimati.
Una volta determinato un costo (e di conseguenza un prezzo di vendita congruo) del prodotto occorre rivalutarlo nel tempo a fronte di eventuali aumenti dei costi componenti, di mutazione del contesto di mercato (es. maggiore o minore concorrenza sui prezzi), introduzione di vincoli normativi, cambiamenti organizzativi (nuovi macchinari, nuovo layout, nuovi stabilimenti,…).
Oggi queste variabili hanno assunto un peso molto significativo ed impongono una rivalutazione molto attenta non solo dei costi, ma anche del metodo di calcolo e dei criteri utilizzati. Infatti, un determinato criterio può essere idoneo se certi parametri variano poco attorno a determinati valori target, viceversa se la variabilità di questi parametri è stata molto significativa, anche i criteri dovrebbero essere rivisti.
Vediamo quindi quali sono le componenti che, sommate fra loro, andranno a costituire il costo finale (costo pieno, secondo la teoria del full costing) del prodotto, prendendo anche in considerazione le esigenze informative che sono richieste al sistema informatico gestionale per supportare l’imprenditore nelle scelte legate al costo del prodotto.
Il primo elemento che si prende in considerazione è il costo del materiale. Esso va, ovviamente, determinato calcolando il peso (quantità) del materiale necessario per realizzare ogni singolo particolare e moltiplicandolo per il costo (al kg o al grammo) del materiale stesso. Tale valore, ideale, dovrà subire parametri correttivi dovuti a diversi fattori:
- Sfridi e scarti di materiale, dovuti anche al fatto che spesso materie prime come, ad esempio, l’acciaio vengono vendute in barre di una determinata lunghezza (e peso) e che l’alimentazione delle macchine automatiche genera delle rimanenze (spezzoni) che non possono essere riutilizzate.
- La fluttuazione dei prezzi della materia prima nel tempo può influenzare il costo del prodotto anche nel breve periodo ed in taluni casi esistono diverse opzioni per la scelta del materiale, di prezzo diverso e spesso anche di prestazioni diverse. L’estrema variabilità (in aumento) dei costi delle materie prime può anche far indurre a ritenere opportuno approvvigionarsi di materiale oggi perché domani il costo del materiale potrebbe essere superiore.
- La gestione dell’acquisto del materiale comporta tempo del personale ed oneri di gestione, compresi costi di immagazzinamento e rischi di obsolescenza. In alcune situazioni questo suggerisce di applicare un piccolo sovrapprezzo sul costo della materia prima. Dovendo sopperire ad una carenza di materie prime (effettiva o prevedibile come in questi tempi) o tempi di consegna estremamente lunghi, probabilmente la scelta più sensata e approvvigionarsi del materiale di cui si pensa di aver bisogno in un periodo sensibilmente più lungo del solito, assumendosi un maggior rischio di obsolescenza nel caso in cui il materiale non venga utilizzato a causa di un calo degli ordinativi previsti nel lungo periodo.
Occorre, infine, tenere presente che talvolta il materiale è fornito in conto lavoro dal cliente, quindi non costituisce un costo per il fornitore che deve comunque gestirne l’immagazzinamento ed i controlli in accettazione, oltre ad eventuali sfridi e scarti di lavorazione.
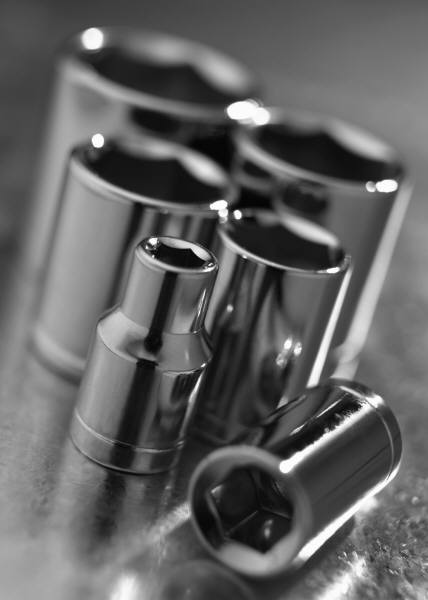
Il secondo macro-elemento da considerare nella determinazione del costo del prodotto è il costo delle lavorazioni, il vero valore aggiunto che fornisce la nostra azienda al cliente. Qui l’azienda si gioca gran parte della propria competitività perché su queste attività c’è la maggior parte del margine aziendale, la ragione per cui il cliente ci ha scelti per realizzare il suo prodotto.
Il costo delle lavorazioni è dato dalla somma dei costi di tutte le fasi di lavorazione – interne ed esterne – comprese nel ciclo di lavorazione e controllo. Le fasi di lavoro si possono suddividere in quattro categorie: lavorazioni interne, lavorazioni esterne, operazioni di controllo ed attività logistiche (imballaggio, immagazzinamento, spedizione).
Ogni fase di lavoro svolta internamente può richiedere o meno una operazione di setup o attrezzaggio macchina – eseguita una volta per ogni commessa di lavorazione, salvo eccezioni – e comprende una lavorazione vera e propria effettuata su ogni singolo pezzo oppure sull’intero lotto produttivo. Dunque, ogni fase di lavoro ha un costo pari a:
[1] Costo fase i-esima = Costo orario di setup x tempo di setup + Costo orario di lavorazione x Tempo di lavorazione.
Da questa scomposizione emerge subito il fatto che mentre il primo addendo è indipendente dal numero dei pezzi lavorati, il secondo cresce proporzionalmente al numero dei pezzi lavorati; pertanto, ai fini del calcolo del costo del prodotto, la componente unitaria del costo di lavorazione della fase i-esima per unità lavorata è dato dal
Costo unitario fase i-esima di lavorazione = Costo di setup/numero di unità lavorate + costo di lavorazione unitario.
Nella formula [1] Il costo orario di setup è costituito da due componenti: il costo orario della macchina ed il costo orario dell’operatore, perché in questa fase sia la macchina, sia l’operatore che la attrezza impiegano contemporaneamente il loro tempo nella fase di attrezzaggio, di realizzazione dei primi pezzi (campione) e nel loro controllo, fintantoché non vengono realizzati particolari pienamente conformi alle specifiche e, quindi, avviene il cosiddetto Benestare Avvio alla Produzione (BAP). Il costo dell’operatore è pari al costo della manodopera di quel livello di specializzazione; infatti, solitamente è il personale più esperto (e meglio pagato) che si dedica all’attrezzaggio delle macchine. Oggi, con l’inflazione 2021 al 4,5% ed una prospettiva per il 2022 sicuramente in crescita, bisogna anche prendere in considerazione che il costo della manodopera possa aumentare a fronte di un aumento salariale che sarà inevitabile nel medio periodo. Il ragionamento è il seguente: se i prodotti al consumatore finale continuano ad aumentare (anche a causa dell’aumento del prodotto della nostra azienda campione), il potere di acquisto del consumatore finale si ridurrà e, quindi, si rischia che acquisti meno prodotti o non ne acquisti alcuni, con immediate ripercussioni sul nostro cliente diretto che ridurrà gli ordinativi e, quindi, diminuirà il nostro fatturato. Dunque, vedrete che se l’inflazione aumenterà ancora in modo sensibile, i contratti di lavoro dovranno prevedere un aumento delle retribuzioni.
Il costo orario della macchina viene invece determinato dividendo il costo complessivo di utilizzo della macchina o TCO = Total Cost of Ownership (costo di acquisto + costi di manutenzione e smaltimento) per il periodo ipotetico di utilizzo, costituito non dal periodo di ammortamento fiscale, ma dall’ammortamento reale, ovvero il periodo di vita stimato della macchina. Il tempo di utilizzo della macchina, espresso in anni e poi convertito in ore di lavoro, dovrà essere corretto con un opportuno coefficiente che rappresenta la quota parte di effettivo lavoro della macchina dopo la sottrazione dei fermi macchina per rotture, manutenzioni programmate ed indisponibilità di lavorazioni o personale che sia in grado di attrezzarla.
Visto che le macchine consumano energia, la quale costa sempre di più, è opportuno rivalutare periodicamente il costo dei macchinari, poiché in certi casi la sostituzione con macchinari nuovi e più performanti potrebbe ridurre i costi di produzione (diretti e indiretti) in misura tale da rendere più conveniente l’investimento di quanto si potesse pensare.
Tutto ciò al netto di valutazioni economico-finanziarie legate all’ammortamento fiscale già terminato, alla possibilità di fare un leasing e/o di sfruttare le agevolazioni per Industria 4.0. In quest’ultimo caso si otterrebbe un ulteriore vantaggio, ossia quello di essere in grado di determinare in tempo reale alcuni parametri ed indicatori della nuova macchina, tra cui l’effettiva disponibilità della stessa, che ci serve per un calcolo più preciso del costo del prodotto come sopra esposto.
Molti imprenditori sono soliti considerare che le proprie macchine lavorino a “x euro all’ora”, ma non hanno ben chiari i meccanismi attraverso i quali si è giunti alla determinazione del costo orario, spesso il dato è fornito dal consulente contabile in base all’ammortamento fiscale o alla rata del leasing, senza considerare fermi macchina e costi di manutenzione, che spesso non sono rilevati in modo preciso.

Il costo del setup di macchina è poi influenzato significativamente dalla variabile tempo: spesso i tempi standard considerati in fase di preventivo per il piazzamento della macchina si discostano notevolmente dai tempi effettivi impiegati per il piazzamento, che raramente vengono rilevati da un sistema di raccolta dati efficiente e preciso. Tornerebbe molto importante il lavoro del c.d. “Reparto Tempi & Metodi” che studia i tempi di lavorazione, presente nelle aziende più grandi. Oggi con sistemi informatici di ausilio alla produzione, in particolare i MES, è possibile avere a disposizione tempi reali di produzione, da confrontare con i tempi standard stabiliti in fase di preventivazione o progettazione del processo.
La disponibilità di tempi di setup e di lavorazione accurati non dipende solo dai sistemi informatici, ma anche dalla disciplina dell’operatore nel registrare puntualmente l’avanzamento delle attività.
Conoscendo i tempi di setup e di lavorazione reali con un buon grado di affidabilità potrebbe aiutare, attraverso tecniche della Lean Production, a ridurre questi tempi conoscendone l’effettivo risparmio in termini economici.
Il costo orario di lavorazione della suddetta formula [1] è costituito, anche in questo caso, dal costo orario della macchina e dal costo dell’operatore, ma mentre il primo elemento è identico al precedente, il secondo dipende dal tempo effettivo di impegno dell’operatore sul centro di lavoro. Nelle moderne lavorazioni meccaniche effettuate con macchine a controllo numerico di ultima generazione l’operatore non ha la necessità di presidiare la macchina ed è impegnato solo nelle attività di caricamento materia prima, controllo a frequenze prefissate di alcuni pezzi, sistemazione dei pezzi lavorati negli appositi contenitori, cambio utensili, gestione degli imprevisti, ecc.. La stima del tempo dell’operatore (generalmente di profilo più basso rispetto a colui che attrezza la macchina ed a chi è dedicato ad operazioni di collaudo) è difficile ed altrettanto complicata è anche la rilevazione del tempo effettivo impiegato dall’operatore. Normalmente è opportuno utilizzare dei parametri fissi, determinati a livello aziendale in funzione del rapporto macchine/operatori. Ad esempio, se in un reparto lavorano 2 operatori che supervisionano e controllano 4 centri di lavoro, si dovrà considerare il costo orario dell’operatore al 50% rispetto a quello effettivo (2 persone/4 lavorazioni). In tutto questo bisogna considerare il costo per i controlli in produzione, effettuati a cadenza prefissata (ad. 3 pezzi ogni 100 prodotti).
Diverso è il caso per lavorazioni eseguite manualmente dall’operatore pezzo per pezzo: in tal caso occorre considerare il costo orario pieno della manodopera come adendo del costo della lavorazione per tutta la durata della stessa.
Anche per la lavorazione la variabile tempo è importante: la determinazione del tempo standard unitario di produzione di un singolo pezzo spesso differisce da dati reali che, se raccolti informaticamente, possono permetterci di elaborare statistiche adeguate sui tempi effettivi di lavoro. Vari metodi di calcolo possono essere attuati per determinare il tempo effettivo di lavorazione di un pezzo: si può considerare la media generale di un numero minimo di lavorazioni, si può escludere dal calcolo del tempo medio il valore minimo e quello massimo (spesso causati da situazioni anomale), si può determinare una media pesata in funzione della dimensione del lotto (lotti maggiori possono fornire stime più affidabili), si può considerare un valore prudenziale dato dal valor medio incrementato della deviazione standard al fine di comprendere comunque la maggior parte delle situazioni e così via.
Altre considerazioni vanno fatte per le lavorazioni quali trattamenti termici o superficiali che richiedono un tempo di setup (dei parametri del processo) inferiore ed un tempo di lavorazione complessivo per l’intero lotto, indipendentemente dalle dimensioni dello stesso, o meglio fino ad un certo limite, oltre il quale è necessario effettuare una seconda lavorazione sulla seconda parte del lotto, raddoppiando così i tempi.
Spesso sono proprio queste le lavorazioni svolte esternamente, il cui costo è predeterminato dal prezzo del fornitore, che varia in maniera discreta/discontinua in funzione del lotto (ad es. fino a 1000 pezzi ho un certo prezzo, da 1000 a 5000 un altro prezzo e così via). Naturalmente, se la lavorazione viene esternalizzata occorre informarsi sull’aggiornamento dei prezzi dal fornitore… anche lui avrà ricalcolato i costi della sua lavorazione!
Molta attenzione è poi necessaria nella stima dei costi per fasi di lavoro particolari quali imballaggio, immagazzinamento, collaudo finale, ecc., nelle quali il costo dell’operatore incide in maniera diversa sul lotto di unità prodotte. Ad esempio, al collaudo finale il tempo dell’addetto è proporzionale al numero di pezzi controllati, non alla dimensione del lotto oppure per l’imballaggio il tempo dipende dal numero di colli realizzati.
Anche i costi dell’imballo (cartone, ecc.) – se non fornito dal cliente – potrebbero essere aumentati e bisogna considerarlo.
Infine, la spedizione potrebbe avvenire a carico del fornitore, quindi la nostra impresa deve ricalcolare anche il costo del trasporto, visto che è aumentato notevolmente anche il gasolio per autotrazione e i costi di trasporto lieviteranno di conseguenza. L’utilizzo di mezzi propri o di spedizionieri/corrieri esterni va considerato nei conteggi.
Dopo aver sommato il costo del materiale e quello di tutte le lavorazioni occorre, per arrivare a determinare il costo pieno del prodotto, stimare i costi indiretti, che dovrebbero costituire una quota minoritaria del costo complessivo, ma talvolta non sono trascurabili, soprattutto in periodi di crisi e di forte variabilità come questo che stiamo vivendo.
Qui nasce il problema di come ripartire fra i vari prodotti/commesse (in gergo si utilizza il termine “spalmare”) tutti gli altri costi non imputati direttamente al prodotto. La regola basilare è quella di non calcolare due volte una parte di costo, né di non coprire tutte le voci di costo dell’azienda.
Le voci di costo che solitamente non sono state attribuite direttamente ai prodotti possono essere raggruppate nelle seguenti:
- Costi di struttura (affitto locali, consulenze, forniture per la struttura, ecc.);
- Costi commerciali (pubblicità e marketing, provvigioni commerciali, spese di rappresentanza,…);
- Costi del personale dipendente non direttamente impiegato nelle lavorazioni (impiegati amministrativi, responsabili ed addetti delle funzioni acquisti, qualità, sistemi informativi, ecc.), considerando anche le quote parte del personale della produzione che non viene impiegato nella produzione stessa per inefficienze, scarso lavoro, ecc.;
- Consumi (energia elettrica, riscaldamento, ecc.), eventualmente depurati dei consumi direttamente imputati ai costi macchina: tali costi, come anticipato, possono essere aumentati di molto e difficilmente prevedibili anche in un medio periodo;
- Materiali di consumo;
- Quote di ammortamento (reali) di beni strumentali e licenze software;
- Tutte le spese non considerate nelle voci sopraelencate.
Alcune semplificazioni possono essere effettuate senza alterare l’accuratezza del risultato. Considerando i costi indiretti e la produzione dell’esercizio precedente si può considerare che i costi indiretti da ribaltare siano una certa percentuale del costo del prodotto, ma occorre la massima attenzione per non incorrere in errori significativi. Poiché, infatti, la maggior parte dei costi indiretti sono anche costi fissi, cioè sono indipendenti dai volumi produttivi, il calcolo suddetto potrebbe essere inficiato da notevoli variazioni nei volumi produttivi, cosa molto frequente in questo periodo di forti variazioni.
Facciamo un esempio: se nel 2021 l’azienda ha fatturato 10.000 (in migliaia di euro) con costi della produzione pari a 6.000 e costi indiretti 2.000 (per un margine di contribuzione lordo pari a 2.000), l’incidenza dei costi indiretti è del 2000/6000 = 33% sui costi della produzione.
Supponiamo che nel 2021 il fatturato cali a 6.000 (-40%) ed i costi della produzione siano pari a 3.600 (sempre il 60% di ricavi), mentre i costi indiretti siano sempre 2.000. Per il 2022 l’incidenza dei costi indiretti sul costo della produzione è 2000/3600 = 56%, dunque quale percentuale consideriamo (33% o 56%) nella determinazione del costo del prodotto nel 2022 se non sappiamo quale sarà l’andamento dell’azienda? In periodi di forti fluttuazioni alcuni schemi di calcolo non sono più validi!
Quest’esempio deve essere considerato non come caso limite, ma come caso reale. Infatti, negli ultimi tempi abbiamo avuto un anno (2020) contraddistinto dall’inizio della pandemia con conseguente lockdown che ha avuto un impatto significativo, anche in termini di chiusure forzate, per molte aziende, con conseguente alterazione dei costi e dei ricavi. L’anno successivo, il 2021, è invece stato contraddistinto da una forte ripresa economica, ma con forti variazioni del mercato delle materie prime e dell’energia; dunque, anche nel 2021 il rapporto fra costi e ricavi potrebbe essere non particolarmente indicativo sull’evoluzione futura.
Altre valutazioni possono essere fatte, ad esempio si può ripartire i costi indiretti sulla base di altri cost driver, come ad esempio il tempo impiegato per produrre un singolo pezzo (comprensivo del tempo di setup della macchina): i costi indiretti possono essere suddivisi per giornata lavorativa e quindi per postazione/centro di lavoro, ottenendo un costo orario indiretto di ogni centro di lavoro, consumato dai pezzi lavorati per il lotto di produzione. Oppure utilizzare il metodo del direct costing per superare il problema.
Poiché i costi dell’energia sono in molti casi considerevoli, potrebbe essere utile affinare il calcolo di tali costi, da un lato introducendo dei contatori dei consumi energetici (energia elettrica e gas) che permettono di conoscere il consumo esatto di ogni centro di lavoro o reparto, dall’altro “far pesare” in modo differente certe fasi di lavoro più “energivore” rispetto ad altre, in funzione del lead time di produzione come esposto in precedenza.
In taluni casi, soprattutto per le aziende del settore automotive, il cliente prima di ordinare la produzione di importanti volumi di articoli, richiede l’approvazione del c.d. PPAP, ovvero una progettazione del processo produttivo per realizzare un nuovo articolo, comprendente anche la preparazione di una serie di documenti (FMEA di processo, certificato del materiale, diagramma di flusso del processo, control plan, ecc.) e la realizzazione di una campionatura di un numero limitato di pezzi. In questi casi il costo del nuovo prodotto dovrà comprendere anche una percentuale legata al costo per la progettazione del processo (se non pagato dal cliente), che andrà “ripartito” sui volumi di produzione che si pensa di realizzare.
Infine, al costo del prodotto, va aggiunto un “piccolo” margine percentuale per determinare il prezzo da formulare nel preventivo. Tale prezzo, nel nostro algoritmo di calcolo, potrà essere variato in modo semplice in funzione di diverse variabili, modificabili a richiesta: costo del materiale, numerosità del lotto, frequenza e numerosità dei controlli, costo manodopera, sostituzione di una macchina per la produzione con un’altra equivalente dal punto di vista tecnico, ma con velocità produttiva diversa, capability differente (e diversa probabilità di generare prodotti non conformi), diversa incidenza dei costi indiretti, ecc..
In conclusione, il calcolo del costo del prodotto è molto articolato e le considerazioni sopra esposte possono variare in realtà diverse. Per ottenere risultati affidabili sono necessarie competenze adeguate (all’interno o all’esterno dell’azienda), sistemi informatici efficienti, rilevazioni dei tempi di produzione precise ed affidabili. Oggi, a maggior ragione per i motivi sopra esposti, è importante che il sistema di calcolo del costo del prodotto, una volta progettato, sia adeguato a fornire risultati immediati al variare dei parametri in input (ad es. costo della materia prima, costo dell’energia, costo orario delle macchine, ecc.). Tale sistema dovrà essere applicato, come detto, non solo alla preventivazione dei nuovi prodotti, ma anche alla riformulazione dei prezzi dei prodotti già a listino. Quest’ultima potrebbe non essere un’operazione semplice perché, a differenza del passato non si può più fare ragionamenti approssimativi del tipo: “la materia prima è aumentata del 10% per cui visto che la sua incidenza media sul costo dei vari prodotti è del 30%, aumenterò il prezzo di tutti i prodotti del 3% (=30% x 10%)”; perché si rischierebbe di sbagliare, finendo fuori mercato con i prezzi oppure rischiando di produrre sottocosto.

Probabilmente il foglio Excel, seppur ben progettato, non basta più perseguire un ricalcolo a tappeto di tutti i costi dei prodotti; inoltre l’integrazione con i sistemi informatici gestionali è fortemente consigliata, per avere dati sempre aggiornati su articoli, listini, prezzi di vendita, prezzi di acquisto, cicli di lavoro e – attraverso l’integrazione con i sistemi di produzione (MES) – anche tempi effettivi di lavorazione, dati sulla qualità del prodotto (pezzi conformi e pezzi non conformi) e sulla disponibilità delle macchine, fino al calcolo dell’indice OEE.